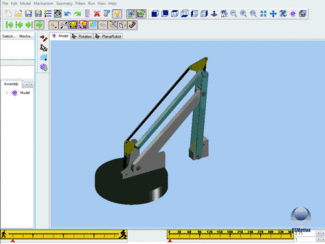
Both forward and inverse kinematics can be combined to design a robot path
This example looks like a lamp! However, it is exactly like a planar pick and place robot but with a base that can rotate. But the example shows another capability of MechDesigner.
When designing a mechanism that has tooling that is at the end of a mechanism, or robot, it is important that you can design the exact motion of the tooling itself. This is why MechDesigner has at its core an inverse kinematics design methodology.
The motion for the tooling is designed first, and then the mechanisms are added. All the design details for implementation are automatically calculated while keeping your important design motions intact.
- Although Inverse Kinematic analysis is preferred for designing packaging machines and mechanisms so that the motion of the tooling is known and predictable, Forward Kinematic analysis can also be used by simply assigning a motion design to another part of the mechanism
- In this example, we used a combination of forward and inverse kinematics to drive the robot's gripper. The pick and place planar robot part had motion designed at the tool while the rotation part was designer on a motor shaft ( because it is so simple )